8月19日下午19:43分,我国首创的油气田海床下开发模式主体结构钢圆筒,成功在渤海海域锦州25-1油田W-1井区安装完成,标志着由中海油研究总院(简称研究总院)牵头研究并独立自主设计的、针对渤海通航区量身定做的海床下开发模式,又向成功迈出了关键一步,为盘活渤海数亿油气产量提供了坚强的技术后盾,对实现油气资源增储上产,保障我国能源安全具有重要意义。
我国首创海床下开发模式
主体结构钢圆筒成功安装
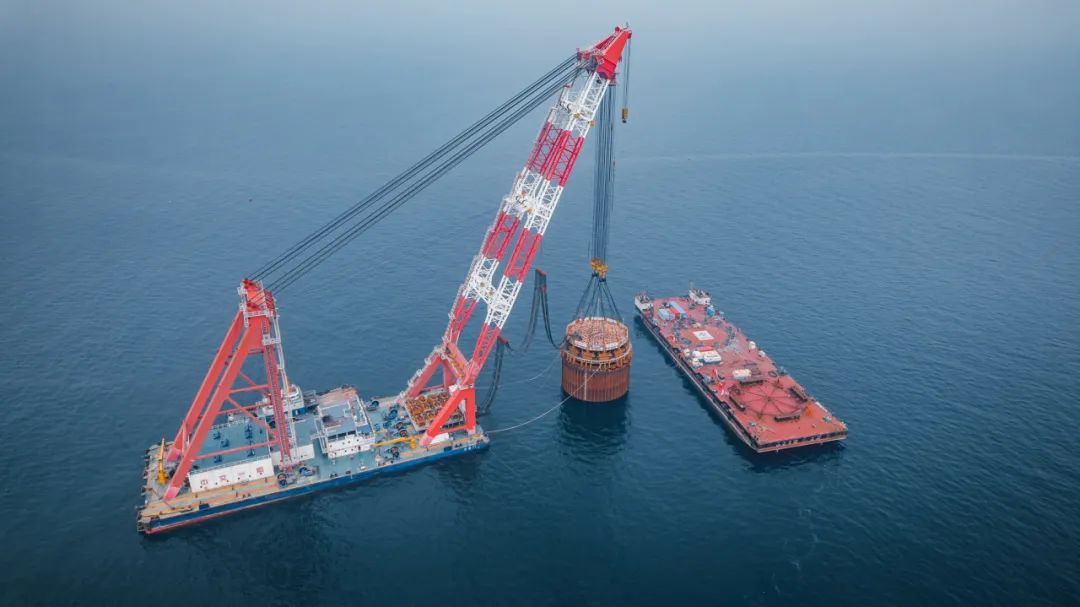
8月19日下午19:43分,我国首创的油气田海床下开发模式主体结构钢圆筒,成功在渤海海域锦州25-1油田W-1井区安装完成,标志着由中海油研究总院(简称研究总院)牵头研究并独立自主设计的、针对渤海通航区量身定做的海床下开发模式,又向成功迈出了关键一步,为盘活渤海数亿油气产量提供了坚强的技术后盾,对实现油气资源增储上产,保障我国能源安全具有重要意义。
钢圆筒体外直径24米,高14.25米,重达450吨,顶部由12台振动锤夹持。钢圆筒入水后,在自重作用下下沉稳定后,12台振动锤同时启动,钢圆筒在海床内缓缓下沉,同时,严格控制并调整筒体的水平度,直到最后一次测探,钢圆筒安装指标完全达到设计要求。
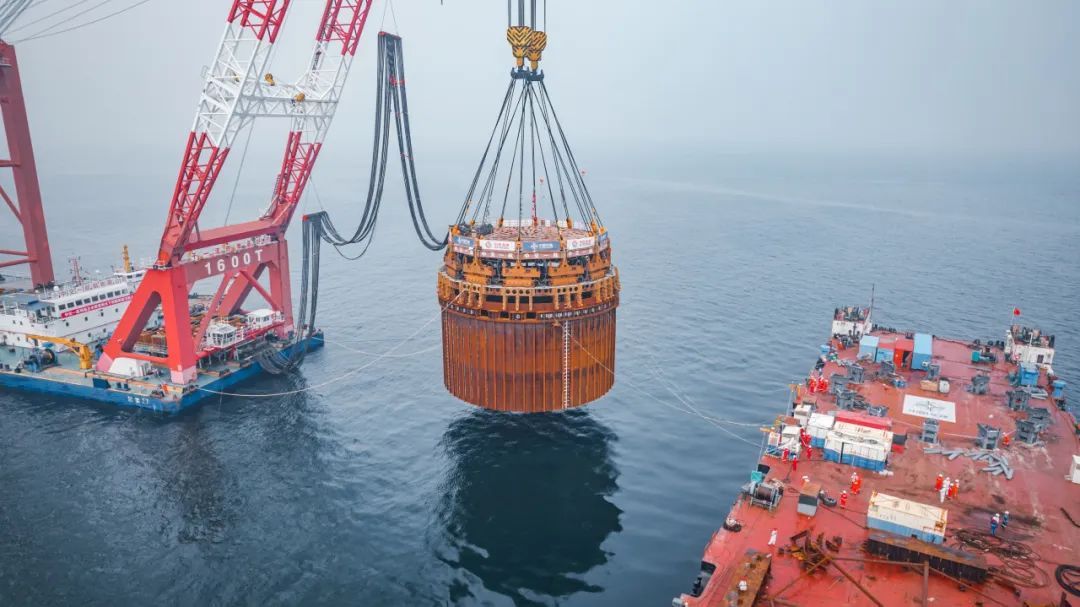
我国油气对外依存度逐渐攀升,已超过60%国际公认警戒线,国家能源安全形势严峻,而渤海区域油气资源丰富,是我国海洋石油的重要产区之一。海床下开发模式,是研究总院精心打造的,一把能够开启渤海通航区油气资源宝库的“金钥匙”。
推动方案创新,用新模式突破环境制约
想要高效开发渤海油气资源,将油气开发设施设置在海床面以下成了唯一的有效途径,这就需要建立一套安全可靠的防护系统保障油气设施安全生产以及后期检修维护。油气开发设施的安全极为重要,一旦发生损坏,泄露的原油将会对环境造成极大的破坏,然而这种开发模式在全球范围内没有先例。整套油气开发设施占地数百平米,净高近十米,如此大的规模,实现起来非常困难。
一开始,研究总院科研人员考虑将油气开发设施全部布置在一个大型的混凝土沉箱中,整体埋进海床里。但是,需要开挖的基坑面积却要达到数千平米,开挖土体工程量近二十万方。有没有一种方法,能够在开挖少量土体的前提下,将防护结构安装到海床下呢?
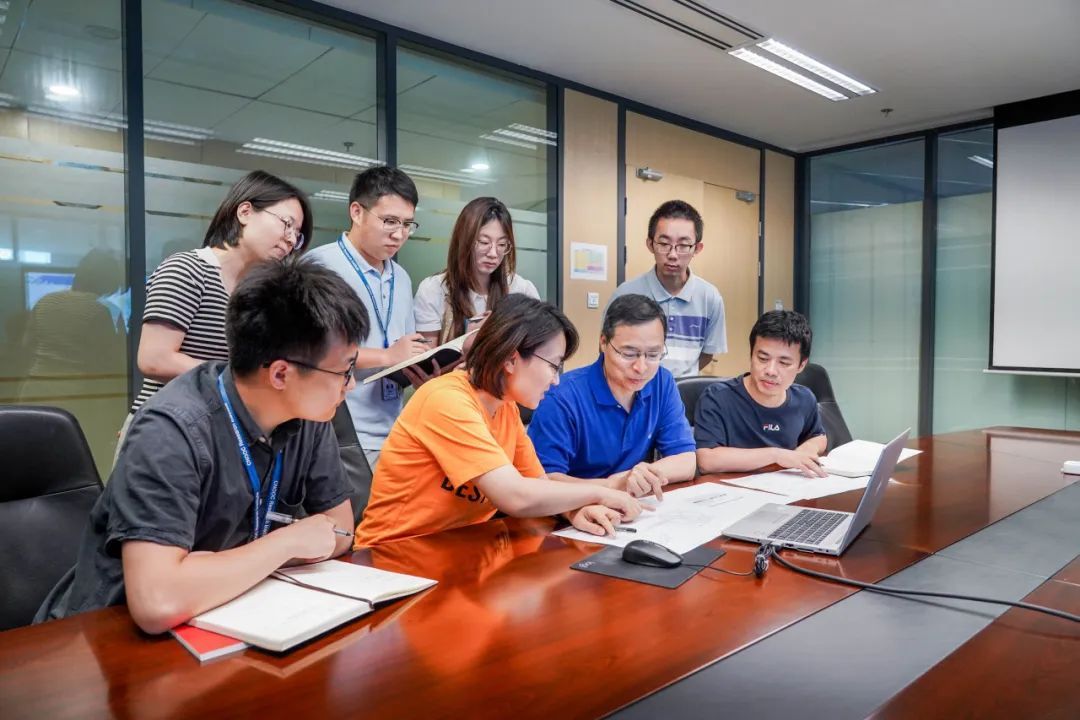
在经过广泛的调研后,国内其他项目建造人工岛时使用的大直径钢圆筒振沉技术,进入了科研人员的视线:通过振动锤带动大直径钢圆筒进行振动,从而降低土体阻力,使大直径钢圆筒在激振力和自重作用下沉入海床。基于此,科研人员研究了多个水下防护方案进行比选分析,对可能存在的每一个选项进行了详细的论证,最后选定防护结构就是这个大直径的钢制圆筒。
科研人员对钢圆筒的结构强度进行了详细分析,确保其可以承受安装和生产期间的所有载荷,从而起到地基支护和水下设备安全防护的双重作用。最终,经过反复的研究与讨论,一体化水下防护结构钢圆筒的方案最终成型。通过振沉技术,将钢圆筒沉入海床,然后将钢圆筒内部的土体挖出,并在其中放置油气开发设施,随后在钢圆筒顶部安装顶盖,防止淤泥及落物的进入筒内。
理论结合实际,技术攻关解决振沉难题
相比大直径钢圆筒以往的应用案例,海洋石油行业有着许多特殊之处。由于采油设备、海底管道等的要求,钢圆筒身上设置有大量支架、开槽,对钢圆筒的安装有着很大的影响。开槽将破坏钢圆筒的完整性,使振沉过程中容易发生结构损坏;而支架则给振沉过程带来了额外的阻力。
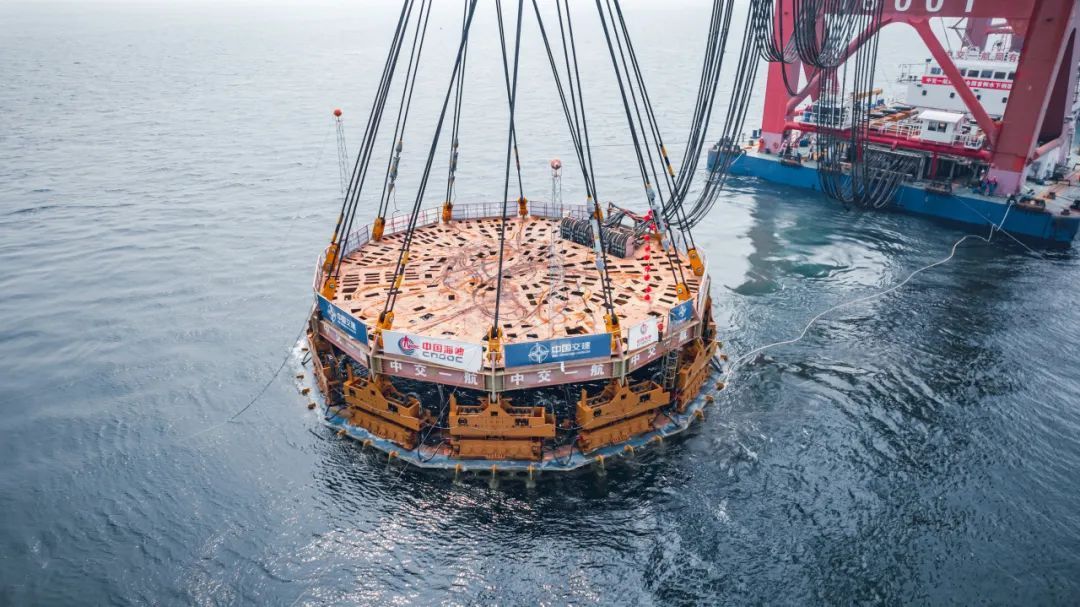
为保证钢圆筒可振沉以及筒体结构安全,科研人员从振沉的基础原理出发,翻阅了国内外振沉相关的大量文献资料,力求追本溯源,积极与国内拥有振沉施工经验的单位开展交流,不局限于以往使用的规范公式,通过攻关,建立了先进的评估钢圆筒可振沉性大变形数值分析技术,同时使用以往工程的实际监测数据,验证设计方法的正确性,通过深入分析,全力确保钢圆筒的可振沉性。
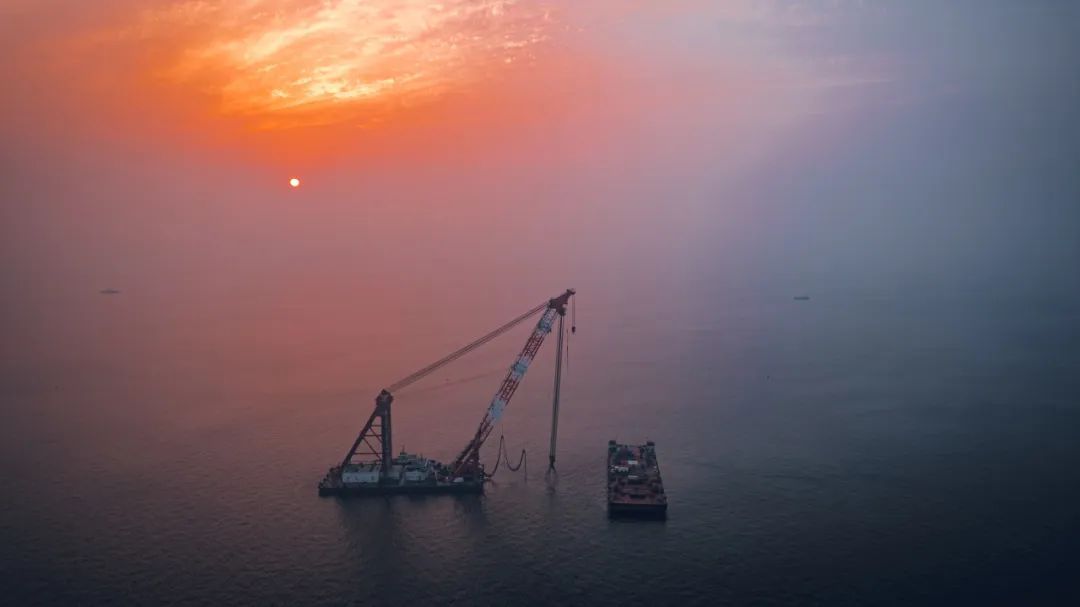
锦州25-1油田W-1井区开发项目是我国首个渤海油气资源海床下开发模式的示范项目,防护主体结构钢圆筒的成功安装,标志着研究总院建立的通航区海床下水下防护结构设计技术安全可靠,为我国通航区的油气资源开发提供了安全的解决方案和强有力的技术保障。从此,渤海通航区油气资源从“看得见,摸不着”变成了一桶桶的原油。海床下开发示范项目的成功,对持续推动我国油气资源增储上产具有重要意义。
(中海油)