近日,“北京东六环超大直径盾构隧道高品质建造科技示范工程”获得交通运输部正式批复。该工程成为本市首个获批的交通运输部科技示范工程创建项目,曾以排名第一的优异成绩通过全国项目遴选初审。凭何领跑全国、甚至超越欧美?超大盾构机突破了哪些核心技术,记者带您解锁盾构机领跑密码。
近日,“北京东六环超大直径盾构隧道高品质建造科技示范工程”获得交通运输部正式批复。该工程成为本市首个获批的交通运输部科技示范工程创建项目,曾以排名第一的优异成绩通过全国项目遴选初审。凭何领跑全国、甚至超越欧美?超大盾构机突破了哪些核心技术,记者带您解锁盾构机领跑密码。
东六环改造工程南起京哈高速立交,北至潞苑北大街,全长约16公里。其中京津公路至潞苑二街段为隧道段,长度9.2公里,为全国在建最长的地下高速公路隧道,盾构段长度7336米,盾构隧道成型外径15.4米,为北方直径最大盾构隧道。
首发建设公司东六环项目处负责人何历超介绍,该工程建成后,北京城市副中心12条规划道路、5条现状道路将实现东西向贯通,可有效缓解东六环交通压力,对促进京津冀区域交通协同发展,提升北京市交通服务水平,构建综合交通体系具有重要意义。
到达正在施工的隧道底部无需徒步,从地面乘坐电梯,再乘坐摆渡车行驶15分钟后,就能到达目前盾构机所在位置。记者走进施工现场,映入眼帘的是一座高大的“地下工厂”,深深的隧道一眼望不到头。西线隧道盾构机“京华号”正开足马力,以每天20米左右的速度稳稳地向前推进,掘进已达6700米。隧道全长7.4公里,预计将于今年年内贯通。
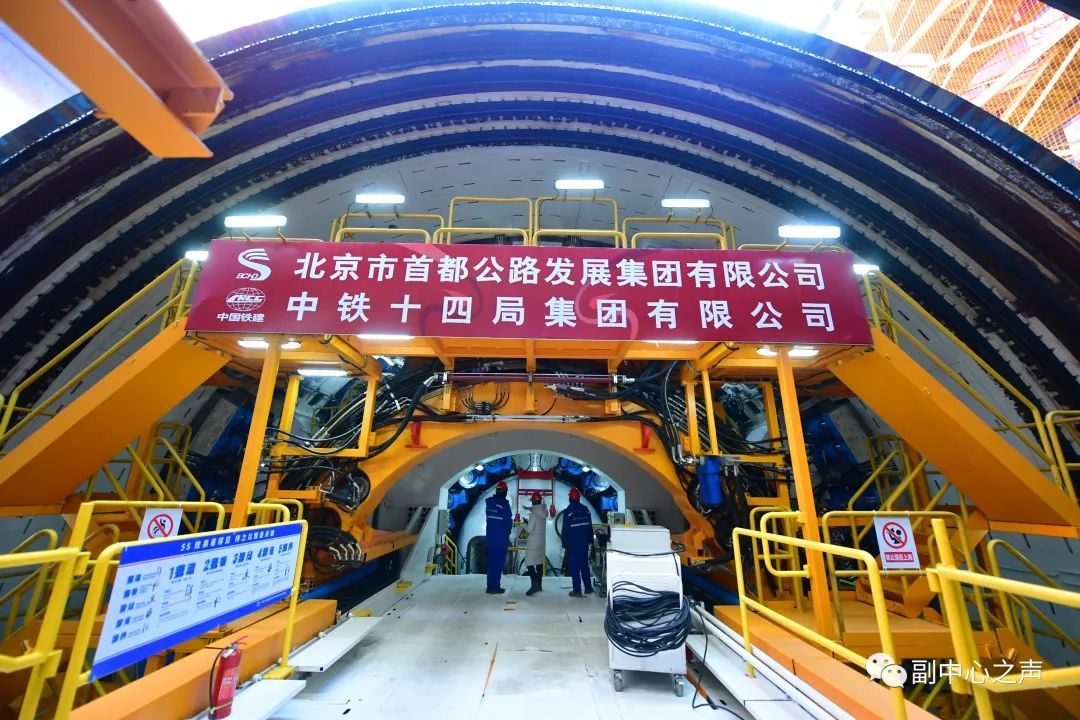
盾构机常压换刀技术历经四代走向国际
中铁十四局北京东六环项目盾构副经理孙长松介绍,“京华号”盾构机,代表了我国相关领域的最高水准。它最大开挖直径16.07米,整机长150米,总重量4300吨。可以说,这个“大块头”的投用,标志着中国超大直径盾构隧道施工依靠国外品牌时代的终结。
“京华号”盾构机高超水平在过去的21个月里得以验证。它先后穿越了京哈铁路、北京城市副中心站综合交通枢纽等几十处风险点,并创造了单月进尺542米的掘进纪录。“如今,中国隧道工程中使用的盾构机90%以上都是国产,让人难以想象的是,就在20年前,中国还没有一台自己的盾构机可以用于这样的工程。”孙长松感慨道。
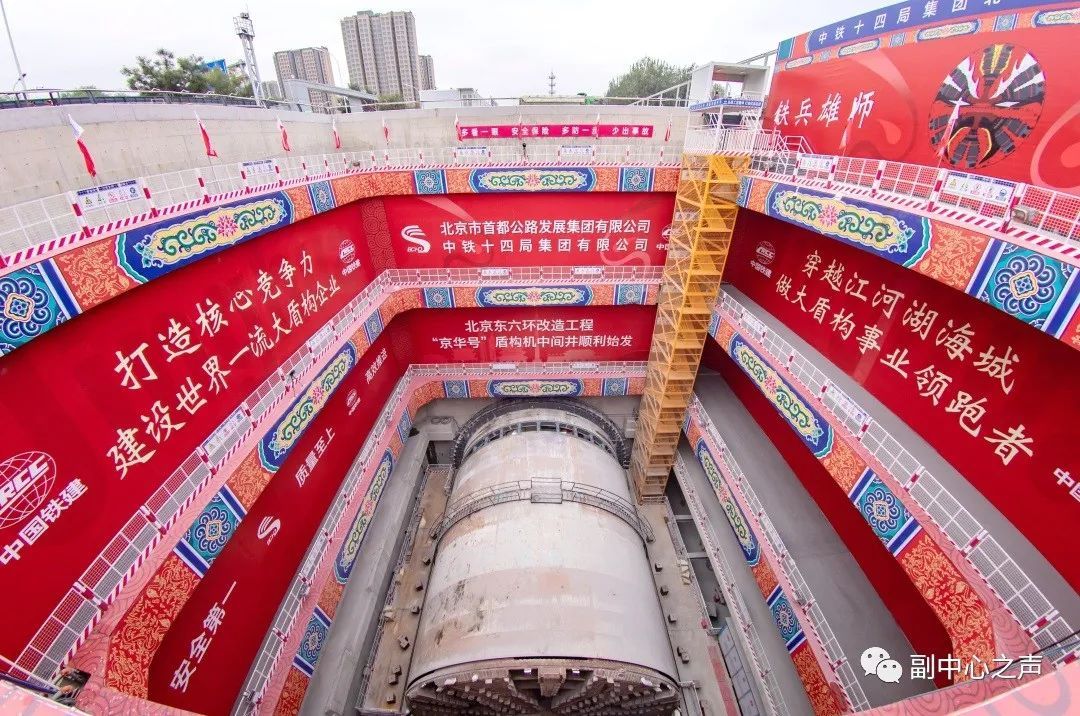
据了解,上世纪90年代末,中国城镇化开始起步,基础设施建设加速。1997年,为了建设西康铁路秦岭隧道,中国第一次进口了两台德国盾构机。盾构机施工不仅效率大幅提升,而且施工过程安全性大大提高。但是,在享受安全高效的同时,中国人也不得不接受高昂的设备费用和并不顺畅的售后服务。
中国施工企业管理协会科技专家、中铁十四局大盾构公司总经理陈鹏见证了中国大盾构隧道井喷式增长速度,在过去的十余年里,陈鹏和他的团队参建了全国超30%的大盾构隧道。“2004年,我参建了南京长江隧道。在建设时,我们要花高价请外国工程师调试设备,安装、维修零部件。外国专家对我们实行技术封锁,不许中方人员靠近,更不用说学习参数计算方法、设备管理理念了。”陈鹏回忆。
试想一下,一台盾构机包含上万个零部件,产业链涉及机械制造、电子元器件、液压管路等多个工业领域,体型巨大、技术精密,若没有强大的集成控制系统,盾构机根本无法正常工作。
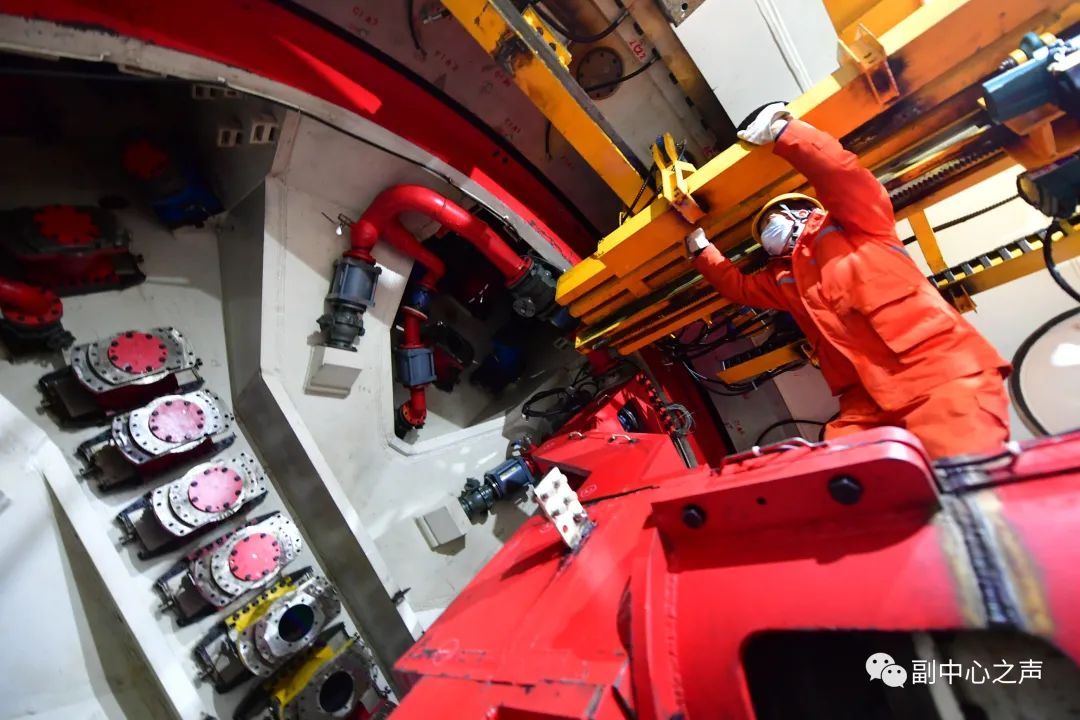
制造盾构机,欧美国家有上百年历史,我国何以能快速实现追赶?业界专家的给出的答案是:施工技术与制造技术相互促进是关键。
专家表示,盾构机研制技术的不断优化,更多来自施工的持续反馈。以盾构机换刀技术为例。在盾构机掘进中,刀具损坏了怎么办?传统的方式是带压换刀,这需要繁琐的加压进舱、减压出舱等操作,耗时长、费用高,还存在安全风险。在施工过程中,技术人员提出常压换刀设想。在南京长江隧道工程中,中铁十四局施工团队联合制造商,调整了盾构机结构,研发并成功试用了第一代常压换刀技术。
2010年,中铁十四局负责施工的南京地铁10号线过江隧道工程,面对复杂的地质和高水压,技术人员联合科研人员重新设计了换刀的结构体系,研发出第二代常压换刀技术——套筒油缸式换刀技术,并首次应用在11米级直径盾构施工中。
创新无止境。在2015年中标的武汉地铁8号线工程掘进中,针对江底不同岩性复合地层的地质条件,中铁十四局施工团队首次开发了滚齿互换式换刀技术,成为第三代常压换刀技术。
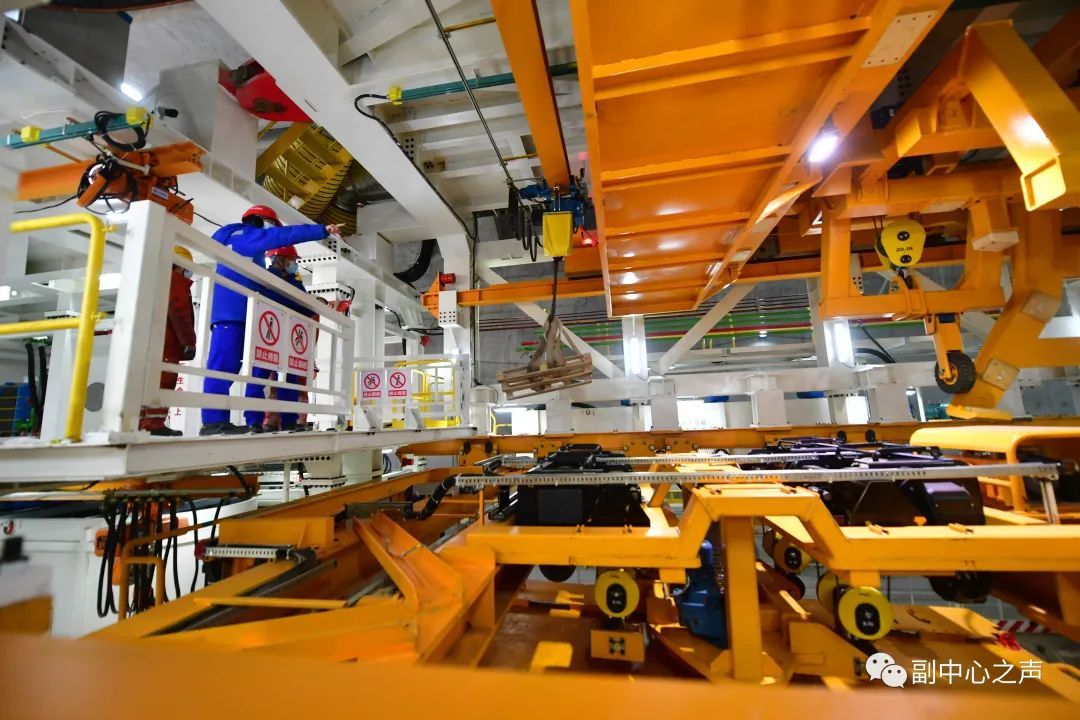
而“京华号”配备的已是第四代常压换刀技术。“它的刀盘上有364个硬质合金制成的刀头,硬度媲美金刚石,最轻的都有200斤。其中,有104把是可以常压换刀的。”孙长松解释称,由于泥水平衡盾构机前面的泥浆循环体系是中空的,以往工作人员常规使用带压换刀的方式,会像“潜水员”一样在压力环境下操作。现在则不同,工作人员可以钻到呈箱体状的刀盘中,把刀头抽回箱体内更换,最快40分钟就能轻松更换刀具,更加安全高效。
从带压到常压,逐代优化,这一从实践中反馈研发、不断提升的换刀技术,如今已成为大盾构研制的常规选项。“我国盾构施工市场需求大,遇到的地质种类多,能够持续反馈,才推动盾构机自主研发快速更新迭代。”陈鹏说。
泥水环流系统成掘进渣土“功臣”
盾构机不断掘进,切削出来的土石怎么清运?记者了解到,在“京华号”巨大的刀盘后面“藏”有泥水舱,掘进中主要依靠泥浆作为支护材料,通过贯穿整台盾构机的送泥管进入到泥水舱。在压力控制下,短时间内可在开挖面上形成不透水的泥膜,用来平衡水土压力,这样就可以保证隧道开挖面的稳定。
而作为泥水盾构主要系统部件的泥浆环流系统,其作用就是在维持开挖面稳定的同时,承担巨量渣土输送,以及对气垫仓、开挖仓和刀盘上不同区域实施大流量、高压冲刷等重要任务。
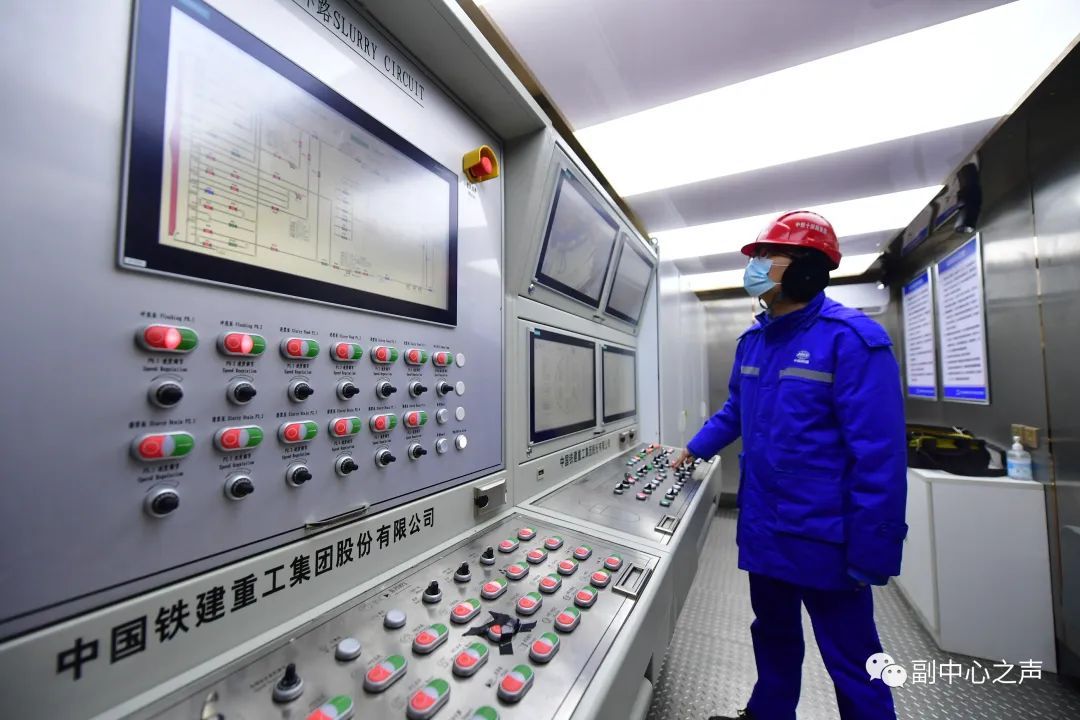
“由于盾构机穿越地层较复杂,尤其是经过软土、上软下硬复合地层及断裂破碎带地层施工时,刀盘结泥饼、堵管、堵泵、堵舱风险较高,处理难度及风险较大。”孙长松表示,盾构机若突然堵塞,压力会瞬间攀升,严重时会造成地层冒顶、泥浆窜出地面或者穿透河底,地层极其的不稳定很有可能会发生坍塌等风险。
为了防止堵塞,中铁十四局依托超级地下工程装备湖南省重点实验室泥浆环流系统试验台,对泥浆环流系统泥水仓不同角度、位置进行模拟冲刷实验,通过系统模型仿真和系统测试对比分析来验证模型数据分析的有效性和准确性,为“京华号”大流量泥水环流系统设计提供数据理论支持。同时,针对不同的泥浆环流工况,还进行流态仿真分析,比对不同冲刷条件下管路磨损情况,配置合理的冲刷流量及管路,保证设备性能稳定。
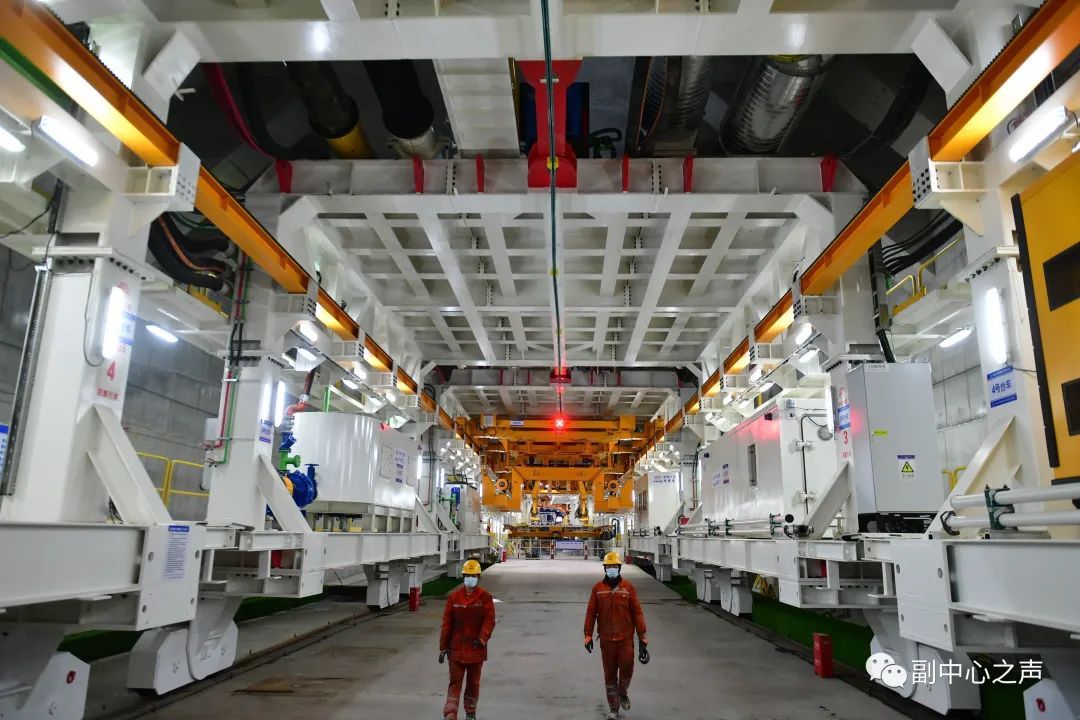
孙长松介绍,泥浆环流系统的正常运转是泥水盾构掘进施工的保障,主要由碎石机、进排泥浆泵、进排泥浆管、采石箱、控制阀门(液动球阀、气动球阀、闸阀等)管路延伸机构、中继泵、地表储浆池等部件组成。经过研究,项目团队对盾构机的泥浆环流系统进行了技术创新,运用开挖仓高精度气液压力平衡控制技术,进一步保证开挖面稳定;采用开挖仓直排、局部内循环和逆洗等泥浆环流模式,运用颚式碎石机,布置安全可靠的外置式泥浆门,避免泥浆滞排;配置设有7路冲刷管路的气垫仓底部冲刷系统,可对碎石机两侧区域、格栅区域、碎石机与泥浆门之间区域和泥浆门底部区域进行实时冲洗,有效解决刀盘结泥饼难题。
同步双液注浆 填补超大直径施工空白
“京华号”盾构机的控制精度远高于国际标准。“京华号”一路掘进,地表沉降基本上始终保持在3毫米以内。而在国际上盾构机施工的标准一般是沉降不超过30毫米,隆起不超过10毫米。
如此优异的成绩不得不归功于中铁十四局历经三年首创的一项技术。“城市内盾构隧道施工要下穿地上密集风险源,因此需要将地表变形有效地控制在最小范围内,降低对风险源的影响。”陈鹏进一步解释说,要想控制地层沉降等,最关键的是盾构施工的注浆工艺。
常规的盾构隧道施工同步注浆采用的是水泥单液浆,存在凝固时间较长、流失量大、不能及时有效控制管片上浮等缺点。为此,“京华号”创新采用了同步双液注浆。“这一关键技术历经3年的探索和实践,经过一年半的方案论证、试验,充分应用了西南交通大学在本领域的前瞻储备,中国铁建重工集团设备制造的经验,为时6个月的人员系统培训,终于取得了成功应用的阶段性成果。”陈鹏说,这一新技术通过改变同步注浆浆液基础材料与配比,改变同步注浆浆液属性,缩短注浆浆体凝固时间,获得早期强度。
施工过程中,与传统浆液相比,“京华号”浆液固结时间从8小时缩到1小时,并能快速达到有效强度,形成对隧道的加固、地层的支撑。而目前这一研究国内尚无先例,世界各国也无完全成熟的研究成果,填补了我国超大直径泥水盾构隧道同步双液注浆的空白。
在全国盾构施工首次应用安装
智能化能源消耗监控设备
整机长150米,总重量4300吨……“京华号”这个庞然大物,不仅仅体现在体积大,其耗电量也极其惊人。
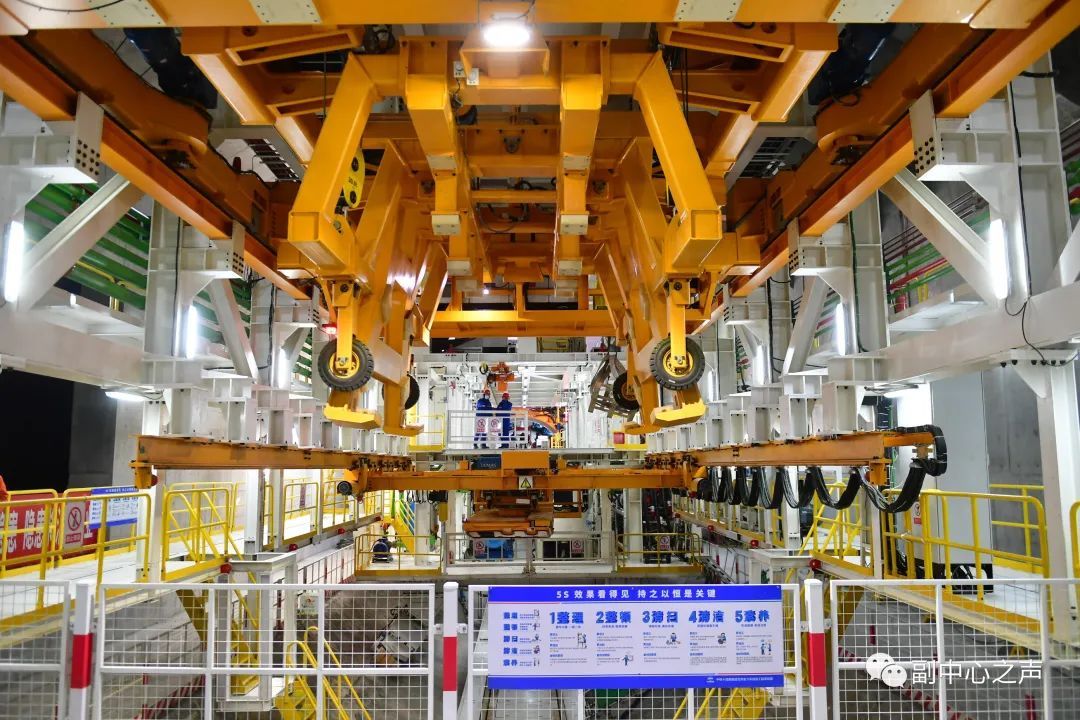
数据显示,北京东六环改造工程现场龙门吊、泥水循环系统、钢筋加工等用电设备达到数千个,整个项目装机功率达到37700千瓦。项目电费可以说是一笔“巨资”。“每一个设备的节约,都是解决跑冒滴漏、实现‘双碳’目标的基础。只有基础做扎实了,才能达到节约的目的,减少不必要的能源消耗。”东六环改造项目调度长张建表示。基于这一目标,北京东六环项目积极探索盾构低碳化施工,与高校共同研发,在全国盾构施工首次加装综合能源智能监测终端和LORA无线自组网通讯终端,对所有的开关站、一级箱等进行能源消耗监控,随时掌握能源使用情况,并在远程设备上进行智能分析,减少不必要的能源消耗。张建告诉记者,该系统通过对所有的10千伏开关站、变压器、配电箱等进行实时能耗数据远程采集,完成变压器负载率计算分析、变压器不平衡度计算分析、功率因数达标分析,指导施工现场调整负荷及投切无功补偿设备,从而提高变压器的运行效率,满足电网对功率因数的考核标准,降低有功、无功损耗。
同时通过该系统可以随时掌握主要设备的能源使用情况,关停不必要的用电设备或合理错峰使用,减少不必要的能源消耗和实缴电费。张建告诉记者,项目在施工现场已安装近百个设备,预估节约电费约200多万元,折合减少碳排放2000多吨。
北京城市副中心报记者:刘薇
摄影:常鸣